焊接機(jī)器人雖然有5-6個(gè)自由度,其焊機(jī)可到達(dá)作業(yè)范圍內(nèi)的任意點(diǎn)以所需的姿態(tài)對(duì)焊件施焊,但在實(shí)際操作中,對(duì)于一些結(jié)構(gòu)復(fù)雜的焊件,如果不將其適時(shí)變換位置,可升降的焊接變位機(jī),就可能會(huì)和焊機(jī)發(fā)生結(jié)構(gòu)干涉,使焊機(jī)無(wú)法沿設(shè)定的路徑進(jìn)行焊接。另外,為了保證焊接質(zhì)量,提高生產(chǎn)效率,往往要把焊縫調(diào)整到水平、船型等佳位置進(jìn)行焊接。
Although welding robots have 5-6 degrees of freedom and their welding machines can reach any point within the operating range to weld the workpiece in the desired posture, in practical operation, for some structurally complex weldments, if their positions are not changed in a timely manner, the adjustable welding displacement machine may interfere with the welding machine's structure, making it unable to weld along the set path. In addition, in order to ensure welding quality and improve production efficiency, it is often necessary to adjust the weld seam to the optimal position such as horizontal and ship shape for welding.
因此,也需要焊件適時(shí)地變換位置。基于上述兩個(gè)原因,焊接機(jī)器人幾乎都是配備了相應(yīng)的焊接變位機(jī)才實(shí)施焊接的,其中以翻轉(zhuǎn)機(jī)、變位機(jī)和回轉(zhuǎn)臺(tái)為多。 前面已經(jīng)說(shuō)了,焊接變位機(jī)與焊接機(jī)器人之間的運(yùn)動(dòng)配合,分非同步協(xié)調(diào)和同步協(xié)調(diào)兩種。前者是機(jī)器人施焊時(shí),河北焊接變位機(jī),焊接變位機(jī)不運(yùn)動(dòng),待機(jī)器人施焊終了時(shí),焊接變位機(jī)械才根據(jù)指令動(dòng)作,將焊件再調(diào)整到某一 佳位置,進(jìn)行下一條焊縫的焊接。
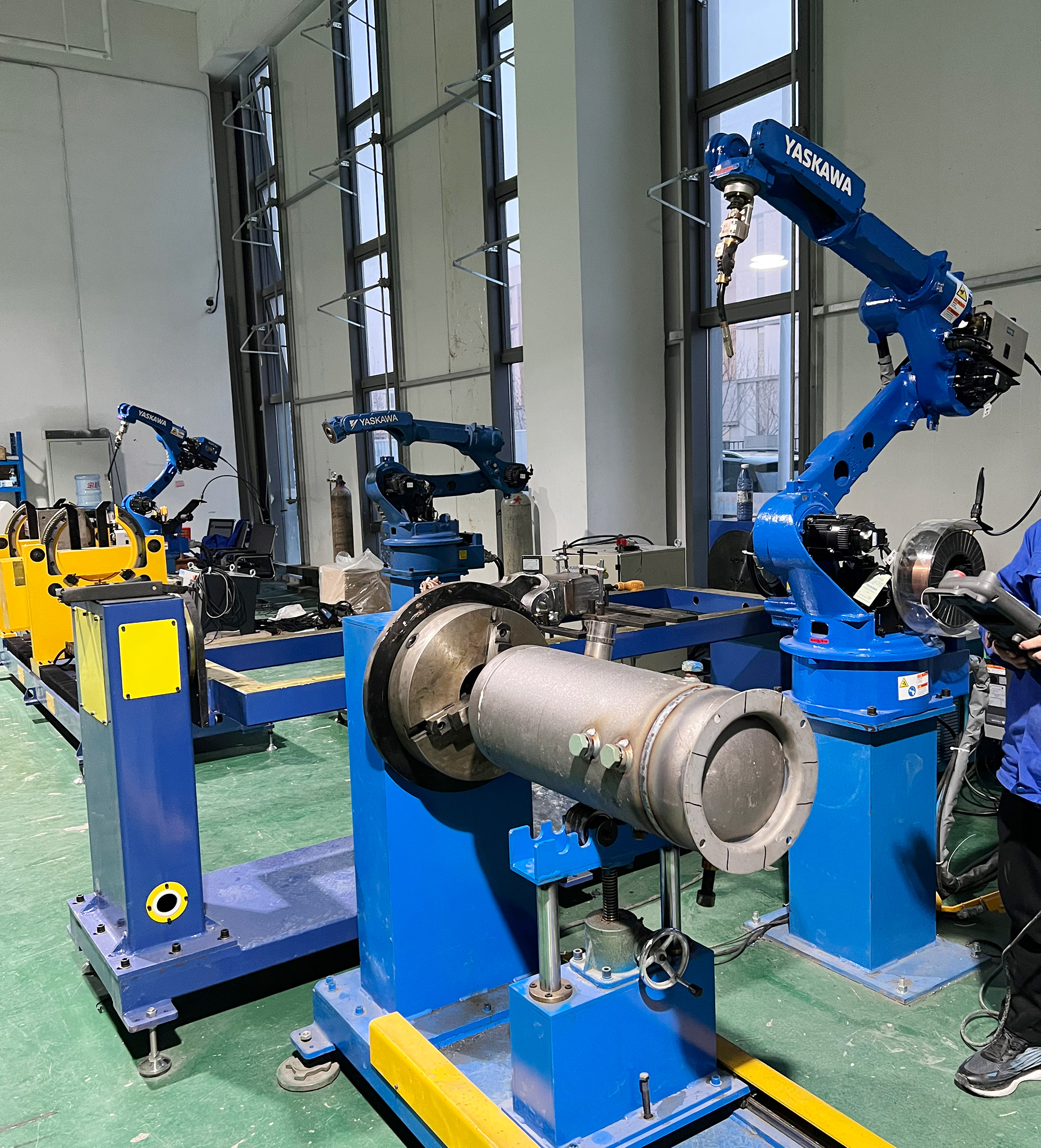
Therefore, it is also necessary to change the position of the welded parts in a timely manner. Based on the above two reasons, welding robots are almost always equipped with corresponding welding displacement machines to carry out welding, with flipping machines, displacement machines, and rotary tables being the most common. As mentioned earlier, the motion coordination between welding displacement machines and welding robots can be divided into two types: asynchronous coordination and synchronous coordination. The former is when the robot is welding, the Hebei welding displacement machine does not move. When the robot welding is completed, the welding displacement machine will act according to the instructions, adjust the welded part to a certain optimal position, and proceed to the next weld seam welding.
如此周而復(fù)始,直到將焊件上的全部焊縫焊完。后者不僅具有非同步協(xié)調(diào)的功能,而且在機(jī)器人施焊時(shí),單立柱回轉(zhuǎn)變位機(jī),焊接變位機(jī)可根據(jù)相應(yīng)指令,帶著焊件協(xié)調(diào)運(yùn)動(dòng),從而將待焊的空間曲線焊縫連續(xù)不斷地置于水平或船型位置上,以利于焊接。由于在大多數(shù)焊接結(jié)構(gòu)上都是空間直線焊縫和平面曲線焊縫,而且非同步協(xié)調(diào)運(yùn)動(dòng)的控制系統(tǒng)相對(duì)簡(jiǎn)單,主機(jī)缸體焊接變位機(jī),所以焊接變位機(jī)與機(jī)器人的運(yùn)動(dòng)配合,以非同步協(xié)調(diào)運(yùn)動(dòng)的居多。
Repeat this cycle until all the welds on the welded part are welded. The latter not only has the function of asynchronous coordination, but also during robot welding, the single column rotary displacement machine can coordinate the movement of the welded part according to the corresponding instructions, so as to continuously place the spatial curve weld seam to be welded on the horizontal or ship position, which is conducive to welding. Due to the fact that in most welding structures, there are spatial straight welds and planar curved welds, and the control system for asynchronous coordinated motion is relatively simple, the welding displacement machine for the main cylinder body is mainly coordinated with the robot in terms of asynchronous coordinated motion.
感謝您的閱讀,此文的文章來(lái)源:切割機(jī)器人更多的內(nèi)容和問(wèn)題請(qǐng)點(diǎn)擊:http://0731b.cn我們會(huì)繼續(xù)努力的為您提供服務(wù),感謝您的支持!
Thank you for reading. The source of this article is cutting robots. For more information and questions, please click: http://0731b.cn We will continue to work hard to provide you with services. Thank you for your support!